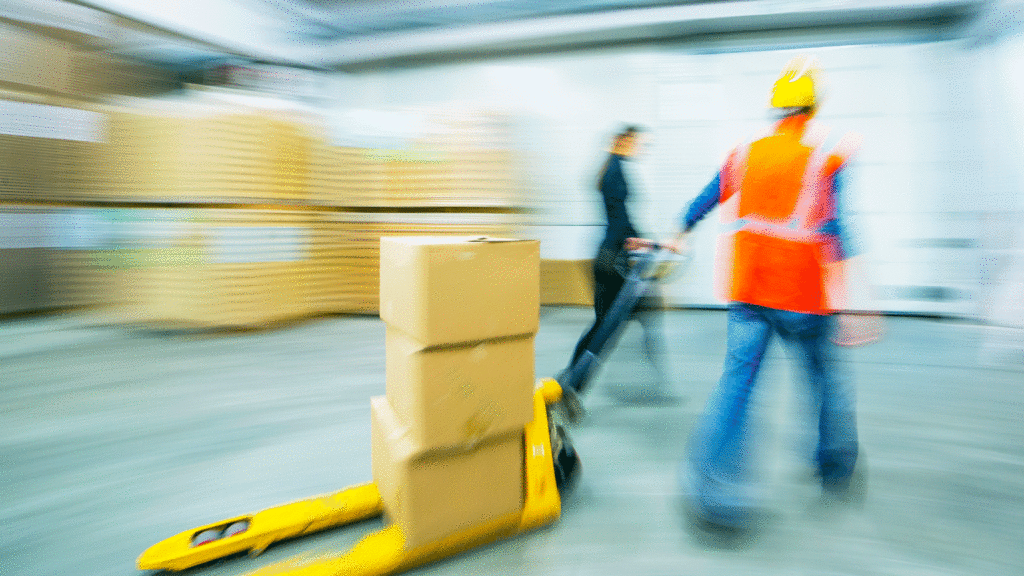
Lean manufacturing concepts have earned their keep in many organizations, and for good reason. They enable companies to get the most out of their resources, increase productivity, and improve profitability.
Sound too good to be true? Fortunately, it’s not.
In an IndustryWeek report titled “The Future of Manufacturing: 2020 and Beyond,” business ranked technology investments based on importance. Lean manufacturing systems were ranked second place, just under quality management solutions.
It’s no surprise that organizations have turned to Lean manufacturing concepts to gain an advantage over their competitors. Top companies like Nike, John Deere, and Toyota eliminated waste and streamlined their manufacturing operations by adopting Lean.
And you can too. Read on to learn more about Lean manufacturing concepts and how to use them to help your organization succeed.
What are Lean Manufacturing Concepts?
Lean manufacturing concepts are designed to maximize delivered value through continuous improvement and minimal waste. Note: While Lean is commonly associated with manufacturing, it can be applied to any industry. Organizations of all sizes have benefitted from adopting Lean manufacturing concepts.
More than a business strategy, Lean is a school of thought that values quality, efficiency, and being innovative.
Lean practitioners understand that optimization is an ongoing process, and the best way to drive continuous improvement is by making incremental and sustainable changes. Lean manufacturing concepts help govern how to make these changes, so you optimize work without disrupting your teams doing the work.
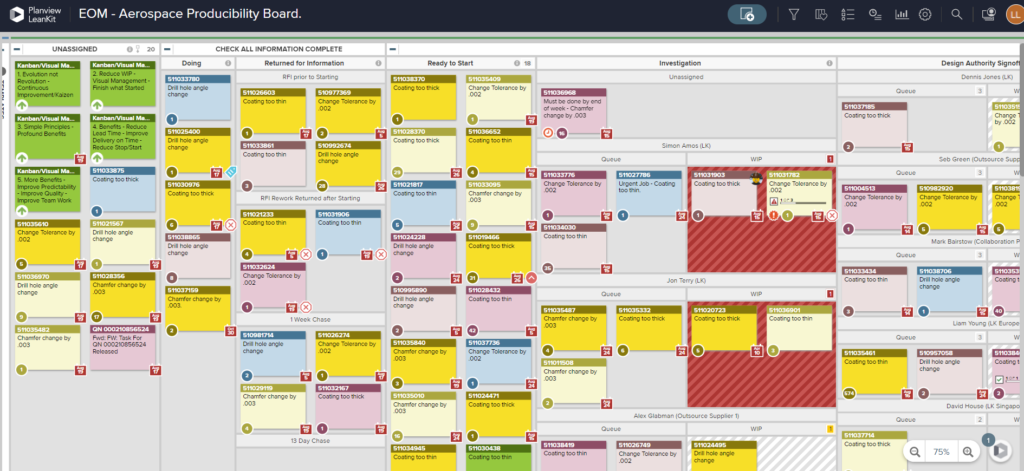
Why are Lean Manufacturing Concepts Important?
It’s not easy for companies to thrive in the modern business landscape. They need to be responsive to customer demands and changes in the market, while also being efficient and cost-competitive.
Before businesses began to adopt Lean principles, efficiency and profitability were often on opposite ends of the spectrum. Organizations typically had to choose between two scenarios:
- Cutting costs and sacrificing operational performance and quality or
- Increasing spending to improve performance and preserve quality
Thanks to Lean manufacturing concepts, companies aren’t forced to choose between one scenario or the other. Lean enables them to simultaneously optimize their operational performance and improve profitability, so they can be efficient and cost-effective. Lean can also be combined with Agile, giving organizations a competitive advantage by helping them become more responsive and efficient.
What are Some Key Lean Manufacturing Concepts?
Organizations draw upon a wide range of Lean manufacturing concepts to help them achieve goals like:
- Eliminating or reducing waste
- Improving quality
- Reducing lead time
- Minimizing unnecessary expenses
One of the greatest advantages of Lean is its flexibility. You can apply its principles to virtually any team working in any industry, provided you’re willing to undertake the Lean journey. It’s not a difficult process, but it requires time and patience.
You can learn more about how to integrate Lean manufacturing concepts by reading our guide on implementing Lean. Below are some important Lean concepts you can integrate into your business operations without extensive effort.
The Customer is First
The goal of Lean manufacturing is to reduce waste without sacrificing the quality of your product or service. Achieving this outcome requires adopting a customer-centric approach that looks at the needs and expectations of the buyer.
Lean manufacturing concepts are more than producing the same product or service faster – Lean is about building quality into every part of the process, while systematically driving out waste from every part of the process, so you deliver a better product or service faster.
A successful Lean organization understands what customers:
- Are willing to pay for
- Value in a product or service
- Expect from a product or service
Staying in touch with consumer expectations is important for two reasons. It lets you know which areas customers aren’t willing to compromise on and what product or service offers they’re not interested in. Understanding this is critical for deciding which parts of your operations are essential, and which elements are considered waste.
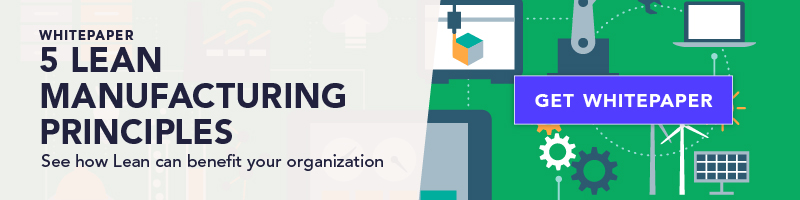
Waste Elimination
Waste takes on a slightly different meaning under the Lean approach. In the Toyota Production System, “waste” is defined using the Three Ms – three terms that together illustrate wasteful practices. Taken from the Japanese language, the terms are muda, mura, and muri.
Organizations that are leveraging Lean manufacturing concepts look at anything that doesn’t bring value to your end product as waste (muda).
- Unnecessary wait times between production steps
- Producing a supply that exceeds customer demand
- Excessive levels of work-in-progress inventory
- Poor logistics
- Inefficient work and idling time
- Defects and poor quality
- Difficulty for workers to move between tasks
- Underutilized workers
Lean manufacturing concepts also recognize two other types of waste:
- Waste caused by fluctuations, such as changes in customer demand or variations with cycle times between workers (mura)
- Waste caused by overburdened workers (muri)
For Lean practitioners, effective waste elimination requires optimizing the entire value stream – i.e., the entire process involved with taking a customer request and turning it into a deliverable product or service – rather than specific areas where wastage occurs.
Process and System Optimization
Process optimization is a part of continuous improvement, also known as kaizen. Kaizen is a core Lean manufacturing concept that’s closely related to waste elimination. It can be defined in two ways: system kaizen and process kaizen.
System or “flow” kaizen applies to optimizing a value stream, whereas process kaizen zeroes in on improving individual processes. When used together, both practices serve to identify waste in multiple forms and make the business more efficient.
Constantly optimizing your processes (and your business as a whole) means identifying and eliminating waste by examining ways to improve repeated tasks.
Optimization opportunities can present itself in several different ways, such as:
- Finding ways to prevent bottlenecks
- Empowering employees through training and team building initiatives
- Staying in touch with customer demand and using that demand to inform your operational performance
The importance of optimization is one of the reasons why Lean manufacturing concepts are so flexible. Lean practitioners accept that processes have flaws and allow organizations to implement flawed processes, provided they’re constantly optimized.
The goal isn’t to create a perfect process or system from the ground up; it’s to regularly improve existing them to maximize efficiency and minimize waste.
Here are four of the most common methods that organizations use to systematically improve their processes, systems, and even their products and services:
- Plan-Do-Check-Act (PDCA) cycle: Based on the scientific method, the PDCA cycle is a technique for change management comprised of proposing, adopting, measuring, and acting on a change to a process.
- A3 problem-solving template: This method condenses all project information onto a single sheet of A3-sized paper. A useful tool for teams, A3 templates include sections for noting the current conditions and root-cause analysis of a problem, and more.
- 5 Whys: The 5 Whys is a powerful tool for solving problems – simply start with the issue at hand, and ask “why” until you determine the root cause.
- Poka-yoke technique: Also known as “error proofing,” poka-yoke is a Japanese term referring to any mechanism in a process or product that helps a person prevent mistakes.
You can read more about other useful Lean manufacturing concepts and tools here.
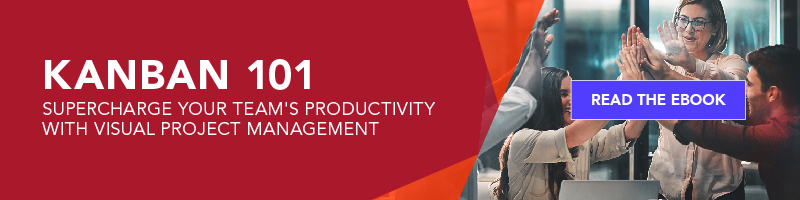
How to Succeed with Lean Manufacturing Concepts
Now that we’ve looked at some core Lean manufacturing concepts, let’s see how you can seamlessly integrate them into your organization.
Map your value streams
Value stream mapping is a Lean manufacturing technique that helps with process optimization. It involves creating a detailed visualization of every step required to take an idea and turn it into a service, product, or value-adding project.
Value stream mapping makes it easier to identify waste in the current operational processes and optimize the way teams work. Organizations seeking to shift from projects to product delivery often map their value streams as one of their first steps.
Implement a Kanban pull system
Traditionally, organizations assigned work based on the push manufacturing system. Under this approach, tasks are pushed onto workers and production is decided by anticipated customer usage. This approach can lead to long wait times, high inventories, and overloaded workers.
The Kanban pull system is a response to problems caused by the push method.
Instead of overwhelming workers with tasks, a backlog of work is created and teams pull assignments based on priority. Kanban boards create transparency by allowing everyone to see which tasks are…
- Sitting in the backlog
- Being worked on by teams
- Completed
- Currently stuck
Pull manufacturing also enables Lean teams to adjust their production based on actual customer demand, rather than anticipated usage – a strategy known as “JIT” or just-in-time inventory management. Inventory is only pulled when it’s needed to fulfill the customers’ orders, which prevents waste in the form of unnecessary work.
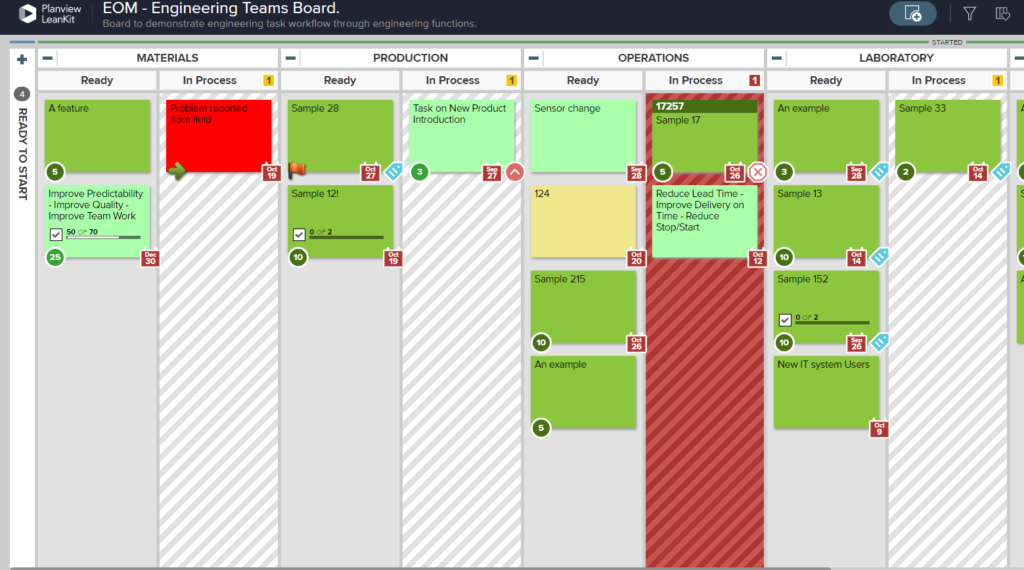
Managers can even choose an optimal pace of work by assigning work-in-progress (WIP) limits on Kanban boards. This prevents teams from taking on too many tasks, which can undermine Lean manufacturing concepts by creating inefficiencies.
Another element of a well-functioning Kanban pull system is the ability for any team member to “pull the andon cord” when problems occur. Also known as “stopping the line,” pulling the andon cord enables team members to immediately signal problems to management and to each other. The practice can identify a range of issues, from a single defect to a systemic problem within the process.
Want to learn more about the benefits of implementing a Kanban pull system? Take a look at our article on why you should switch to one.
Go to the Gemba
Gemba is a Japanese word meaning the “actual place.” For Lean practitioners, going to the Gemba means going to the place where teams are working.
The only way for leaders to truly understand how to facilitate continuous improvement is to understand how teams are working, the challenges they’re experiencing, and how teams are addressing those challenges.
It’s important for Lean leaders to routinely foster relationships with employees, create a culture of respect and teamwork, and learn more about the perspective of teams working on the ground. This helps Lean leaders make informed decisions, in addition to creating a workplace culture that promotes Lean manufacturing concepts.
5S the workplace
5S is a workplace methodology that’s designed to create a working environment that promotes continuous improvement and efficiency. It’s named 5S because it’s a five-step method, consisting of the following steps:
- Sort: Determining which workplace tools are and aren’t needed
- Set in order: Arranging items into their optimal places
- Shine: Cleaning, inspecting, and maintaining the workspace
- Standardize: Create standards that ensure repetition and consistency
- Sustain: Implement a system that encourages long-term use of the 5S method
This approach eliminates waste by helping teams become more organized and aware of their surroundings –– which can reduce time spent looking for tools and other workplace items.
The fourth S, standardize, has broader implications in Lean manufacturing. The concept of “standardized work” refers to identifying and documenting processes so team members know precisely what needs to done and when, empowering them to work efficiently and independently on routine tasks.
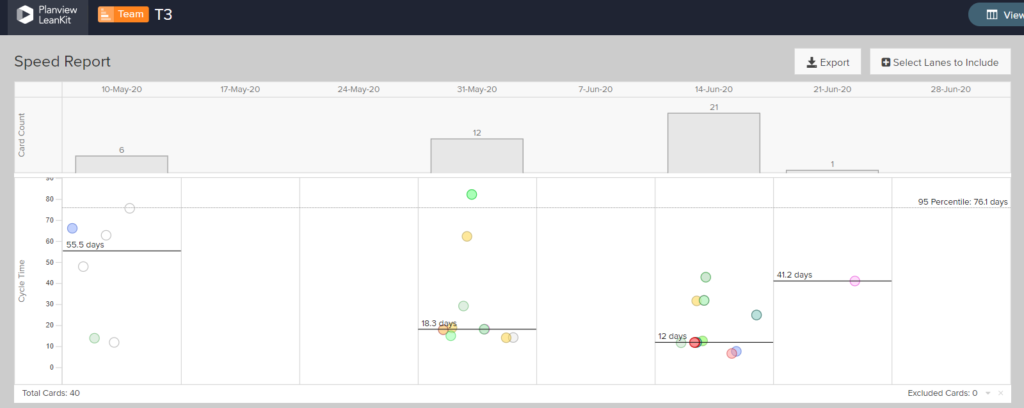
Measure and improve
By now, you already know that Lean manufacturing concepts promote continuous improvement. This requires measuring performance, making changes, and looking at whether those adjustments enhanced the way teams deliver value.
You have to measure performance to determine whether your initiatives are driving improvement. That’s where Lean metrics are helpful. While there are several options to consider for your team, here are a few practical examples: Blockers, queues, and throughput help you look at how work is moving through your system, whether employees are working efficiently, and how you’re reducing waste and driving continuous improvement.
You can learn more about the benefits of Lean metrics and how you can use them to measure and improve performance by reading this post.
Starting Your Lean Journey
Adopting Lean manufacturing concepts can transform the way your company delivers value by creating a sustainable culture that prioritizes efficiency and improvement. Planview AgilePlace can help you get the most out of your Lean journey by giving your organization the tools necessary to collaborate, measure performance, and optimize processes to support work as it moves through the value stream.
Try Planview AgilePlace today and see how easy it is to create a workplace culture that values and follows Lean manufacturing concepts.