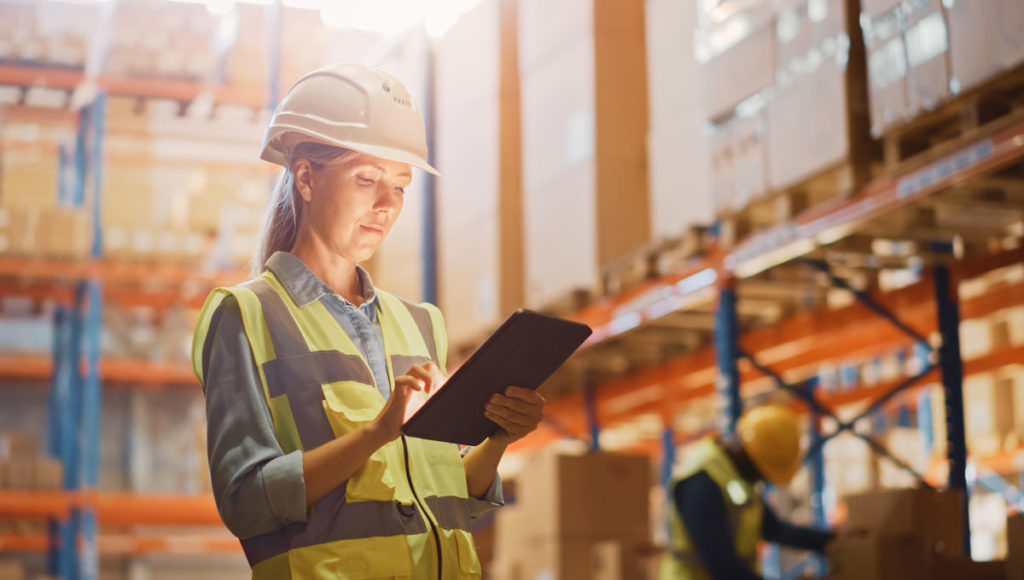
As a global leader in medical technology grew in size and complexity, it struggled to achieve the manufacturing agility required to perform at scale. That’s when Planview AgilePlace became part of their story. With Planview AgilePlace, the company’s globally distributed teams are able to connect strategy to delivery, plan and replan with agility, and empower their teams to focus on what really matters: Improving the lives of the patients they serve.
“Planview AgilePlace has come to be recognized as an application that is used globally at every single manufacturing site we have, as well as the majority of all of our satellite offices around the world.”
Sr. Receiving Inspection Technologist, Global medical technology organization
Agile Mindset Drives Medical Innovations
Manufacturing agility is a benefit caused by Agile and Lean manufacturing — a set of practices, principles, and tools that enable companies to respond swiftly to customer needs and market demands while maintaining quality and controlling costs. It requires not only a mindset that embraces failure, but also a commitment to continuous improvement and iteration so that breakthrough ideas can thrive.
Thoughtful collaboration, incremental progress, and a patient-first approach, have remained at the core of the company’s culture throughout its rich history.
This global medical technology company has prioritized those values in their culture since the beginning. Achieving and maintaining manufacturing agility over decades, in an industry that is rapidly changing, is no small feat: It requires vision, incremental improvement, and, of course, the right tools for the job.
Inefficient Whiteboards Limit Manufacturing Agility
In 2018, the warehouse team at the corporate headquarters in the Western United States was experiencing a serious roadblock to agility: They had been using physical whiteboards to track their workflow, creating a ripple effect of issues.
“[External teams] …had no clue what was happening. You would just know that it’s in the warehouse, being worked on, and that’s about it.”
Sr. Receiving Inspection Technologist, Global medical technology organization
First, critical information was constantly at risk of being erased or changed in error. One accidental swipe of an eraser could permanently delete vital information the team needed to track internal work orders.
Also troubling: The information also couldn’t be shared in a timely way, causing bottlenecks in productivity.
Finally, outside teams, according to the senior receiving inspection technologist we interviewed, “…had no clue what was happening. You would just know that it’s in the warehouse, being worked on, and that’s about it,” he remarked.
Creating Workflow Visibility
The team decided to sign up for a free trial of Planview AgilePlace, and never looked back. With Planview AgilePlace, the team found a centralized system that enabled them to visualize their workflow and share notifications automatically in real-time.
“Ideally, that’s the environment we wanted to create. A place where our programs and applications are communicating and working together so that our employees are being more effective.”
Sr. Receiving Inspection Technologist, Global medical technology organization
Being able to communicate in real time across teams was a manufacturing agility game changer: “Maybe it’s an R&D team asking for an update on a work order,” or floor operators communicating issues to engineers, “…it closed our communication gap,” says the technologist.
Among the essential features for the warehouse team was Planview AgilePlace’s ability to quickly integrate with existing applications. The technologist points out, “Ideally, that’s the environment we wanted to create. A place where our programs and applications are communicating and working together so that our employees are being more effective.”
Connecting Global Teams
Implementing Planview AgilePlace was a huge win for the small receiving warehouse team. Simply by switching their physical whiteboards for Planview AgilePlace boards, the team was able to reduce their work-in-process (WIP) by a whopping 70% – which caught the attention of some higher-ups in the company.
“Management saw the amount of money we’re saving because we were able to improve our process. We were able to quickly quantify that there is something here with Planview AgilePlace.”
Sr. Receiving Inspection Technologist, Global medical technology organization
“Management saw the amount of money we’re saving because we were able to improve our process. We were able to quickly quantify that there is something here with Planview AgilePlace,” he continues.
At the end of 2018, the company had purchased 77 licenses of Planview AgilePlace. By the end of 2019, that number had grown to 227 licenses, across R&D, audits, labs, projects, manufacturing, and other departments.
Fast-forward to 2020, a devastating year that saw many companies forced to furlough or reduce employees because of COVID; the company prioritized innovation and growth, making significant investments in R&D and expanding its team to nearly 15,000 worldwide. And while the spirit of innovation remained a central philosophy to the business, the traditional methods of collaboration necessary to pursue those aims faced entirely novel challenges imposed by the pandemic.
“Remote work, working from home, you have all these teams looking for a method to communicate with each other to track their work,” says the technologist. Luckily, he knew just the tool to suggest: Planview AgilePlace.
With Planview AgilePlace, teams are not limited by the need to be physically co-located around a whiteboard. They can share critical information about work status, requirements, and more through Planview AgilePlace boards customized to mirror their workflows, unlocking greater manufacturing agility than ever before.
“Planview AgilePlace has come to be recognized as an application that is used globally at every single manufacturing site we have, as well as the majority of all of our satellite offices around the world,” he emphasized.
Globally Distributed, Always Connected
Distributed across 100-plus countries, the company’s team is more connected than ever, with more than 617 licenses and counting.
Over 170 cross-functional boards are now being used by microbiology labs to track and communicate test samples, chemistry labs to share status and historical data of test results, the Audit Board to track audit requests, and recently, the HR team adopted Planview AgilePlace adding to the groundswell of support throughout the global organization.
This company is just one of countless success stories showing how digital Kanban boards can help organizations eliminate waste, improve workflow efficiency, and unlock manufacturing agility. Discover more success stories in the Planview Resource Center.