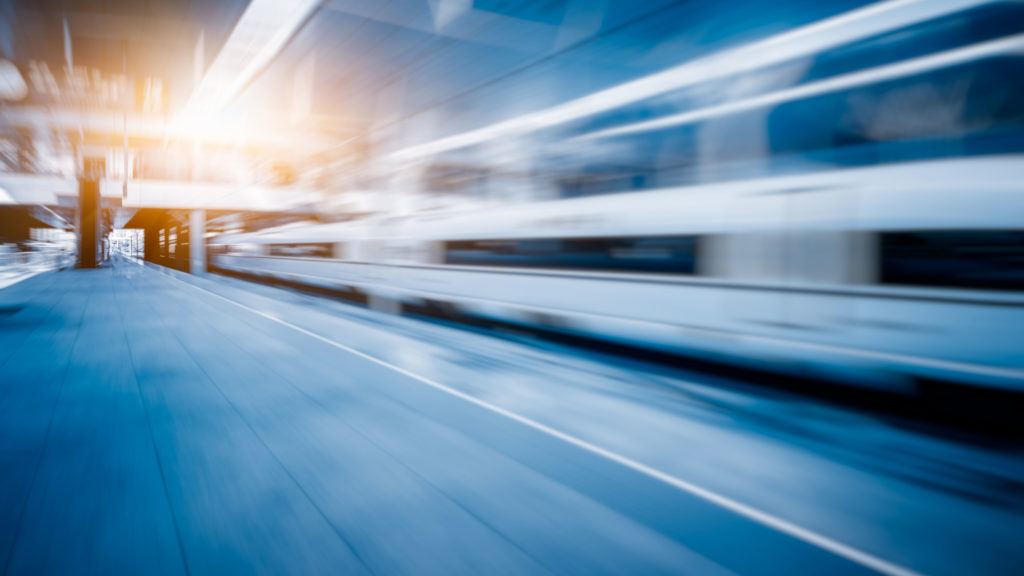
What is Lean Transformation?
Lean transformation is a term used to describe the strategic, tactical, and operational improvements that organizations undergo in order to create more value for their customers. These improvements represent a fundamental, collective shift in business mentalities away from traditional business practices toward a more value-driven, streamlined approach.
There is no single approach to Lean transformation: In some organizations, Lean begins as a grassroots effort, led by a single team or department, and eventually spreads throughout the organization. In others, the call for Lean transformation comes from the top, and involves a strategic, coordinated effort to embrace Lean practices, principles, and business structures.
However, the goal for all Lean initiatives tends to be consistent: To enable organizations to sustainably deliver more value for their customers.
Why is Lean Transformation Important?
In the fast-paced, ever-evolving world we live in, the ability to deliver value efficiently and predictably is more important than ever. And the efficient, predictable delivery of value is what Lean is all about.
Lean transformation enables companies to make that fundamental shift from surviving to thriving by removing those organizational structures, practices, and modes of thinking that inhibit the efficient delivery of value.
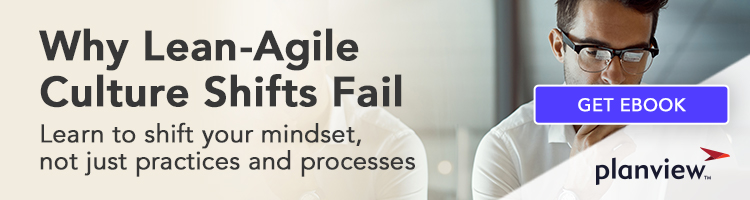
The Lean Transformation Model
Although not every organization approaches Lean transformation in the same way, there are five key components that all successful transformations share. They are:
- A value-driven purpose
- Continuous process improvement
- Sustainable capability development
- Lean management system
- Lean thinking, mindset, assumptions
Value-Driven Purpose
Organizations turn to Lean out of a desire to be able to consistently, predictably create and deliver more value with less waste. This is the fundamental purpose that drives all Lean transformations.
It’s important to define value in the Lean sense: Value, in Lean, refers to any activity, process, product, or outcome that benefits the customer.
Anything that does not add value to the customer is considered waste. This single concept should be a driving force of the entire Lean transformation, and the lens through which all decisions are made.
Continuous Process Improvement
Another fundamental Lean concept is the idea of continuous improvement—more specifically, continuous process improvement. Continuous process improvement is far more difficult to achieve in practice than it might seem, because it requires organizations to embrace experimentation—which means, occasionally, embracing failure as part of the learning process.
The PDCA (Plan-Do-Check-Act) cycle is frequently used in Lean organizations to provide structure to continuous improvement efforts. Similar to the scientific method, the PDCA cycle involves developing a hypothesis, creating a plan to test that hypothesis, analyzing the results of that test, and then implementing any learnings. You can learn more about PDCA and other Lean tools in this article.
Sustainable Capability Development
If you think of an organization as a human body, capability development is like strength training—building and maintaining muscles that can be utilized to meet the organization’s needs.
Lean organizations promote sustainable capability development by:
- Hiring a diverse workforce
- Promoting from within the organization
- Encouraging and sponsoring Lean education
- Creating opportunities for professional development within the organization
- Promoting diversity of thinking and healthy conflict
Low turnover can be seen as a key indicator of effective capability development.
Lean Management System
Lean leadership is servant leadership. Throughout a company’s Lean transformation and beyond, the role of leaders isn’t to tell teams what to do, but to unify teams around a shared goal, and then eliminate any obstacles preventing them from achieving it.
Leaders are called to spend more time “in the trenches” with teams, so that they can truly understand the issues teams are facing, and add value by helping to resolve those issues.
Another key element of Lean leadership is a commitment to being data-driven in decision making: To consistently create and deliver real value, opinion has to give way to fact. It’s up to Lean leaders to reinforce a scientific, and data-driven approach to work.
Lean Thinking, Mindset, Assumptions
Finally, a successful Lean transformation requires a shift in thinking, mindset, and assumptions—together, all of these elements combine to create organizational culture.
Changing the culture of any organization is difficult, and does not happen overnight.
Some of the key cultural shifts that have to occur in order to complete a Lean transformation include:
- Internalizing Lean thinking
- Prioritizing the creation of value over the generation of profit
- Embracing experimentation and failure; celebrating learning over “wins”
- Committing to a data-driven approach to decision making
- Encouraging horizontal communication; amplifying voices across the organization
- Transforming the role of leadership; abandoning the idea that the highest-paid people have the best ideas
- Encouraging transparency and accountability; discouraging “politics”
Phases of a Lean Transformation
Now that you know the components of a typical Lean transformation, let’s unpack a way to look at the phases of a Lean transformation — the steps that an organization needs to take in order to enact sustainable change.
Evaluation
In this first step, organizations evaluate their needs, take inventory of their current organizational structures, and assess the approach they plan to take to their Lean transformation (launch a few teams and then spread, or top-down?)
This is a time to answer big-picture questions about the goals and purpose of the Lean transformation:
- What are the needs driving us to pursue Lean transformation?
- What are the underlying problems that we hope to address through transformation?
- What are our initial and eventual goals for transformation?
Initiation
The next step is initiation — a time to secure executive buy-in, identify Lean champions, and launch educational programs to get everyone on the same page about what Lean is, what the goals of the transformation are, and what will be involved in the transformation.
Training
Next comes training — an essential part of a successful transformation. Some organizations will choose to bring in external Lean experts to guide them through this critical stage in their transformation. Training involves broader education across the organization around key Lean principles and practices.
In addition to learning key Lean concepts — such as continuous improvement and respect for people — it’s important to specifically address how to operationalize these concepts in daily work. Team members need to understand how these Lean principles can be utilized in their everyday lives — and how organizational structures might change to better align with the organization’s Lean goals (this is called Lean portfolio management — learn more about that here).
Tooling
Practicing Lean at scale calls for greater levels of visibility than most organizations are accustomed to; it’s through this visibility that higher levels of accountability and performance are achieved. But without the tools to enable this visibility, many Lean transformations fall flat.
The right tools can make all the difference. Enter: Enterprise Kanban. Kanban is a visual workflow management method that enables the visibility, flexibility, and accountability needed for a successful Lean transformation.
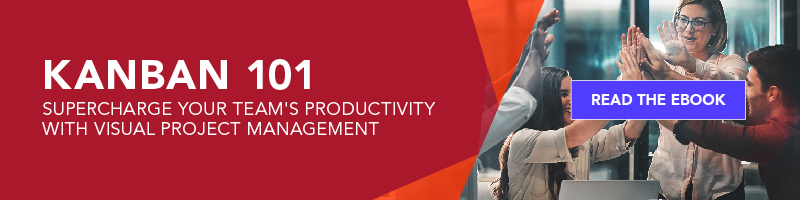
Value Stream Mapping
You know that the goal of any Lean transformation is to orient the organization around the creation of value. Often, this involves not only changing how teams think about their work, but evolving the very structure in which they operate.
Value stream mapping is an organization-wide exercise in which companies:
- Identify how value flows (or fails to flow) through their organization currently
- Determine an “ideal state” to work towards, in which the organization is organized into cross-functional teams around specific value streams
You can learn more about value stream mapping in this article.
Continuous Improvement
Continuous analysis and optimization of the new value streams, and the structures around them, is the next step. As the organization matures in its Lean transformation, and cultural shifts start to take root, it will be able to enter the final step of continuous improvement.
Mature Lean organizations exist in a permanent state of continuous improvement — always searching for ways to adapt, improve upon, and evolve existing practices, processes, and structures to enable more value creation.
How to Start a Lean Transformation
The first step to starting a Lean transformation is identifying the goals of the transformation:
- What are the needs driving us to pursue Lean transformation?
- What are the underlying problems that we hope to address through transformation?
- What are our initial and eventual goals for transformation?
Clarity and buy-in around these fundamental questions will be key to success with your Lean transformation.
Why Does Lean Transformation Fail?
You might be surprised to hear that 70% of transformations fail. Why is this the case with a Lean transformation? Most often, it’s because the transformation simply doesn’t go deep enough. Organizations implement surface-level changes, perhaps adopt some Lean lingo, and call their transformation complete.
Lean transformation is largely cultural, and cannot be faked: The power of Lean transformation is only realized when concepts like continuous improvement, respect for people, and relentlessly focusing on value become a part of the organization’s DNA.
You can learn more about why Lean transformations fail, and how to promote real cultural change in your organization, in this post.
Getting Started with Lean
Every organization wants to sustainably deliver more value to their customers—but not every organization is willing to undergo the deep, cultural transformation required to make it happen. If you’re looking for a quick fix, Lean transformation is not going to be your answer. But if you’re ready to put in the effort to truly transform your organization from within, download our ebook: Getting Started with Lean.