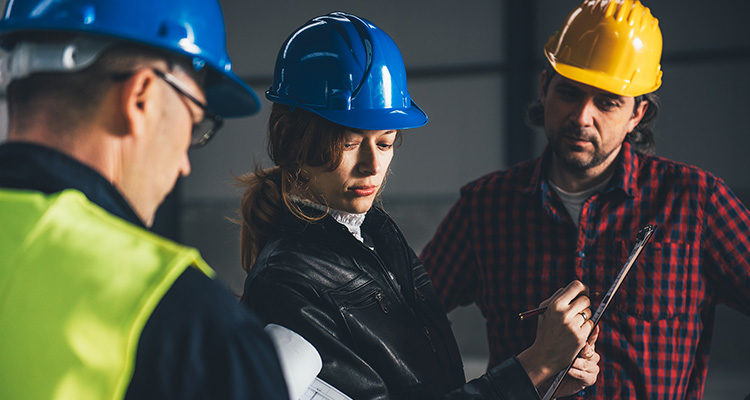
In a complex manufacturing environment, knowing who is doing what, when and how can be cumbersome – especially if you have numerous stakeholders involved in different project phases. Whether trying to get a product to market swiftly or ensuring a smooth roll-out of safety standards, more and more manufacturing organizations are turning to cloud-based project collaboration solutions.
From small projects to global initiatives, project collaboration technology can help manufacturing companies execute and get things done, smoothly and efficiently. When trying to organize, identify, plan and schedule work, it is important to choose the right software solution to ensure people, ideas, systems, and data come together seamlessly.
In Project Collaboration: Use Cases for Manufacturing, we discuss how companies are using technology to create order out of chaos and integrate work silos. Some of the scenarios we review include:
- Scenario #1: Product development – Dealing with multiple stakeholders can be tricky during product development. A cloud-based, project collaboration solution can simplify communication. The result: time is saved and risks are reduced as all project contributors are part of a cohesive team.
- Scenario #2: Implementing new safety regulations and standards – Transmitting and sharing large amounts of data can create a lack of visibility when rolling out new safety standards. Using a cloud-based, project collaboration solution, users around the globe can log in to securely share documents. The result: internal and external stakeholders have one central platform to manage safety regulations.
Read Project Collaboration: Use Cases for Manufacturing to further examine the impact of project collaboration.